New Energy Battery Module Pack Assembly Line
12~24 [PPM] Total capacity
≥99.5 [%] Final excellent rate
≥90 [%] Machine utilization rate
Technical Parameters
Main Parameters | Model |
New Energy Battery Module Pack Assembly Line | |
Total capacity | 12~24PPM |
Final excellent rate | ≥99.5% |
Machine utilization rate | ≥90% |
Overall dimensions | Module assembly line: 58*7.5m Pack assembly line: 100*8m |
Power Supply | Three-phase 380V, 50Hz/60Hz |
Competitive Strengths
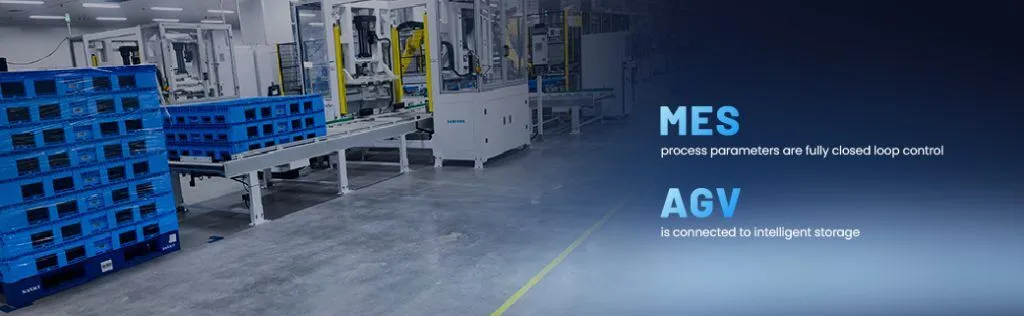
⇲ Reasonable Design
* Front to end automation from assembly, gluing, welding, testing to other key processes
* Its modular-based structure is easy to maintain and keep its running more stable and reliable
* Compatible with various products (fast switch among them), and allow for customization based on customer needs.
⇲ Technological process
* Battery module assembly line
Cell loading & scanning→cell OCV testing→cell/end plate cleaning→gluing or pasting→module stacking→module banding→heating and standing→dielectric voltage withstand test→post terminal addressing→CCS installation→busbar welding→post-weld dust removal→post-weld detection→EOL testing→MES system
* Battery pack assembly line
Pack loading and cleaning & insulating strip pasting→Installation & air-tight test for liquid cooling plate→Pack gluing→Module incasement→Module fastening→Wiring harness copper busbar installation→BMS installation→Top cover installation→Communication cover plate installation→Air-tight test for entire pack→EOL testing→Pack unloading→MES system
⇲ Key spare parts at high quality
* Key components are made of special materials to make sure of their high quality.
* Tooling fixtures are reasonably designed to keep battery cells stable and safe during assembly.
* Advanced laser welding machine can ensure welding quality between battery modules, protect them well and minimize welding defaults.
* Advanced coating/gum topping equipment are used to firmly connect and seal battery modules, in addition, make these modules more resistant to water and dust.
⇲ Safety measures
* Come with safety switch and safety light curtain to prohibit the opening of safety door in operation, and shut down automatically while opening.
* Safety devices such as fuse protector and temperature sensor are installed in battery system to promptly cut off power in case of battery cell abnormality.
* Take strict control of battery charging and discharging to avoid overcharging, over-discharging, and short circuit, so as to keep battery safe.
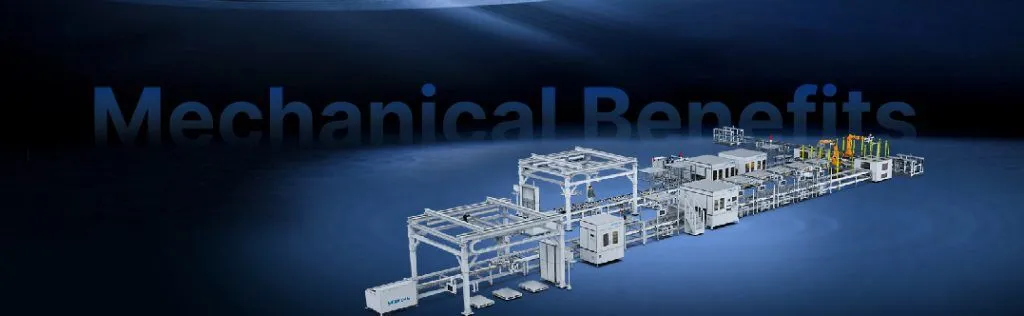
⇲ Reasonable Design
* Front to end automation from assembly, gluing, welding, testing to other key processes
* Its modular-based structure is easy to maintain and keep its running more stable and reliable
* Compatible with various products (fast switch among them), and allow for customization based on customer needs.
⇲ Technological process
* Battery module assembly line
Cell loading & scanning→cell OCV testing→cell/end plate cleaning→gluing or pasting→module stacking→module banding→heating and standing→dielectric voltage withstand test→post terminal addressing→CCS installation→busbar welding→post-weld dust removal→post-weld detection→EOL testing→MES system
* Battery pack assembly line
Pack loading and cleaning & insulating strip pasting→Installation & air-tight test for liquid cooling plate→Pack gluing→Module incasement→Module fastening→Wiring harness copper busbar installation→BMS installation→Top cover installation→Communication cover plate installation→Air-tight test for entire pack→EOL testing→Pack unloading→MES system
⇲ Key spare parts at high quality
* Key components are made of special materials to make sure of their high quality.
* Tooling fixtures are reasonably designed to keep battery cells stable and safe during assembly.
* Advanced laser welding machine can ensure welding quality between battery modules, protect them well and minimize welding defaults.
* Advanced coating/gum topping equipment are used to firmly connect and seal battery modules, in addition, make these modules more resistant to water and dust.
⇲ Safety measures
* Come with safety switch and safety light curtain to prohibit the opening of safety door in operation, and shut down automatically while opening.
* Safety devices such as fuse protector and temperature sensor are installed in battery system to promptly cut off power in case of battery cell abnormality.
* Take strict control of battery charging and discharging to avoid overcharging, over-discharging, and short circuit, so as to keep battery safe.
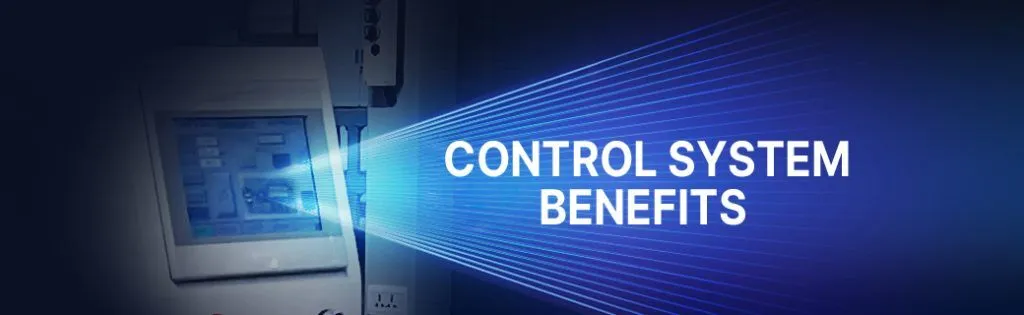
⇲ Collect messages quickly
* It can collect key parameters from each process in real time by using advanced sensor, RFID and wireless communication technology.
* The messages above are transmitted to central control unit for rapid treatment and analysis.
* These messages will be intelligently monitored and analyzed to make sure of safety.
* It also records production process and key parameters, in order to trace back quality and issues.
⇲ Take integrated control
* Its full automation is benefit from advanced automation equipment and technology, which can get efficiency gains and reduce errors and safety hazards caused by manual intervention.
* The system collects, delves into and analyzes big data from production, then, optimizes production processes and parameters based on data analysis results.
* The control system is compatible with various products and allows for further upgrades as need.
⇲ Real-time display
* The system monitors and shows welding parameters, visual inspection, testing parameters, pressure and displacement in real time at work.
* It works with MES system, laser coding and RFID technology to track data for each product.
* At work, machine status is visualized and message interaction is made possible, so, operators are able to check its running state in real time.
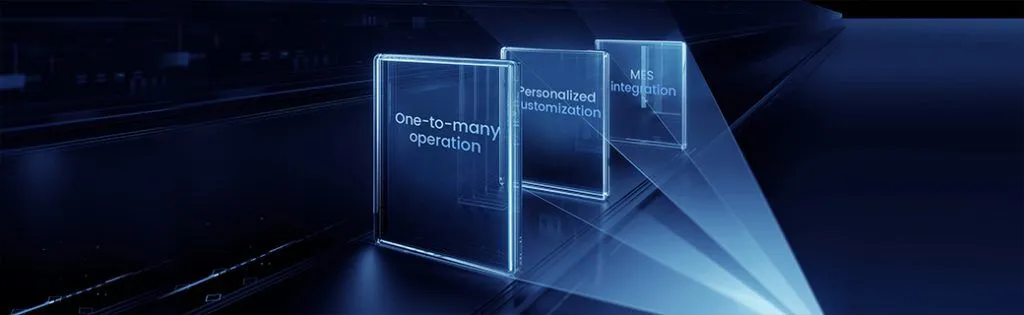
⇲ Intelligent extension
* Due to its modular-based structure, users’ personalized demands and other optional functions are also available.
* New materials and processes are permitted to use to make the production highly efficient. New welding technology also helps to get efficiency gains and high quality.
* Low-energy and low-emission devices or processes can also be utilized to minimize effect on environment and make resources recycling.
Recent Posts
Archives
Categories
Related Products
12~24 [PPM] Total capacity
≥99.5 [%] Final excellent rate
≥90 [%] Machine utilization rate
Equipment Capacity: 12~24 PPM
Overall Line Yield: ≥99%
Overall Line Utilization Rate: ≥98%

Hak Cipta © 2025 Senfeng Laser Technology Co., Ltd. Semua Hak Dilindungi Undang-Undang
Tautan terkait
Hubungi Kami
Alamat:Ruko Golf Island Blok E no 80. Kecamatan Penjaringan, Daerah khusus Ibukota Jakarta
Recent Comments