New Energy Battery Cell Assembly Line
Equipment Capacity: 12~24 PPM
Overall Line Yield: ≥99%
Overall Line Utilization Rate: ≥98%
Technical Parameters
Main Parameters | Model |
New Energy Battery Cell Assembly Line | |
Total capacity | 12~24PPM |
Final excellent rate | ≥99% |
Machine utilization rate | ≥98% |
Power Supply | Three-phase 380V, 50Hz/60Hz |
Competitive Strengths
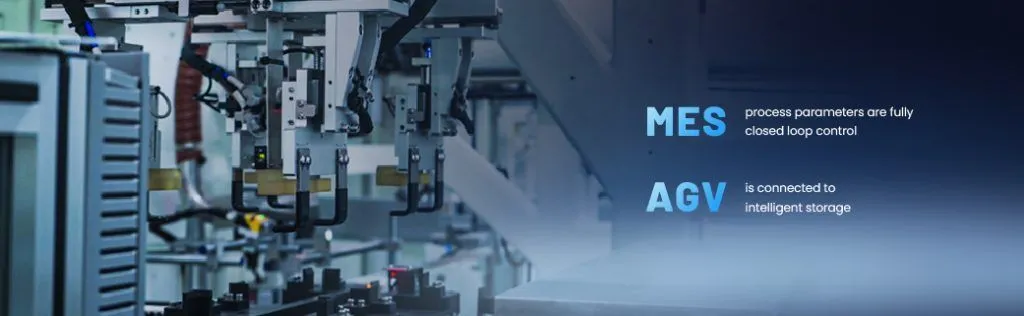
⇲ Reasonable design
* The entire line is designed in accordance with relevant design and technological standards to support diversified demands.
* Efficient logistics methods are employed to ensure fast moving and switch of battery cells at each workstation.
* Advanced control technologies and all-round dust removal measures are adopted to keep battery cell assembly clean.
* Compatible with various battery cells (fast switch among them), and allow for customization based on customer needs.
⇲ Technological process
Preheating→hot pressing→insulation testing→tab cutting→ultrasonic welding→adapter laser welding→welding inspection→cell assembly→coating-heating→cell inserting can→laser pre-welding→laser full welding→weld inspection→insulation testing→leakage testing
⇲ Key spare parts at high quality
* Key components are made of special materials to make sure of their high quality.
* Tooling fixtures are reasonably designed to keep battery cells stable and safe during assembly.
* Laser welding machine with annular laser spot can ensure welding quality and make battery cells much safer.
* Precision moving device, thanks to high degree of automation and intelligent control, can enable accurate positioning and fast assembly of battery cells.
⇲ Safety measures
* Come with safety switch and safety light curtain to prohibit the opening of safety door in operation, and shut down automatically while opening.
* Safety devices such as fuse protector and temperature sensor are installed in battery system to promptly cut off power in case of battery cell abnormality.
⇲ Reasonable design
* The entire line is designed in accordance with relevant design and technological standards to support diversified demands.
* Efficient logistics methods are employed to ensure fast moving and switch of battery cells at each workstation.
* Advanced control technologies and all-round dust removal measures are adopted to keep battery cell assembly clean.
* Compatible with various battery cells (fast switch among them), and allow for customization based on customer needs.
⇲ Technological process
Preheating→hot pressing→insulation testing→tab cutting→ultrasonic welding→adapter laser welding→welding inspection→cell assembly→coating-heating→cell inserting can→laser pre-welding→laser full welding→weld inspection→insulation testing→leakage testing
⇲ Key spare parts at high quality
* Key components are made of special materials to make sure of their high quality.
* Tooling fixtures are reasonably designed to keep battery cells stable and safe during assembly.
* Laser welding machine with annular laser spot can ensure welding quality and make battery cells much safer.
* Precision moving device, thanks to high degree of automation and intelligent control, can enable accurate positioning and fast assembly of battery cells.
⇲ Safety measures
* Come with safety switch and safety light curtain to prohibit the opening of safety door in operation, and shut down automatically while opening.
* Safety devices such as fuse protector and temperature sensor are installed in battery system to promptly cut off power in case of battery cell abnormality.
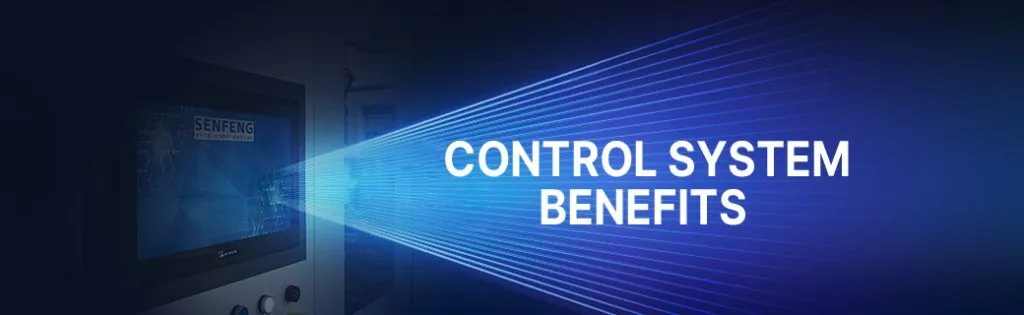
⇲ Collect messages quickly
* It can collect key parameters from each process in real time by using advanced sensor, RFID and wireless communication technology.
* The messages above are transmitted to central control unit for rapid treatment and analysis.
* These messages will be intelligently monitored and analyzed to make sure of safety.
* It also records production process and key parameters, in order to trace back quality and issues.
⇲ Take integrated control
* Its full automation is benefit from advanced automation equipment and technology, which can get efficiency gains and reduce errors and safety hazards caused by manual intervention.
* The system collects, delves into and analyzes big data from production, then, optimizes production processes and parameters based on data analysis results.
* The control system is compatible with various products and allows for further upgrades as need.
⇲ Real-time display
* The system monitors and shows welding parameters, visual inspection, testing parameters, pressure and displacement in real time at work.
* It works with MES system, laser coding and RFID technology to track data for each product.
* At work, machine status is visualized and message interaction is made possible, so, operators are able to check its running state in real time.
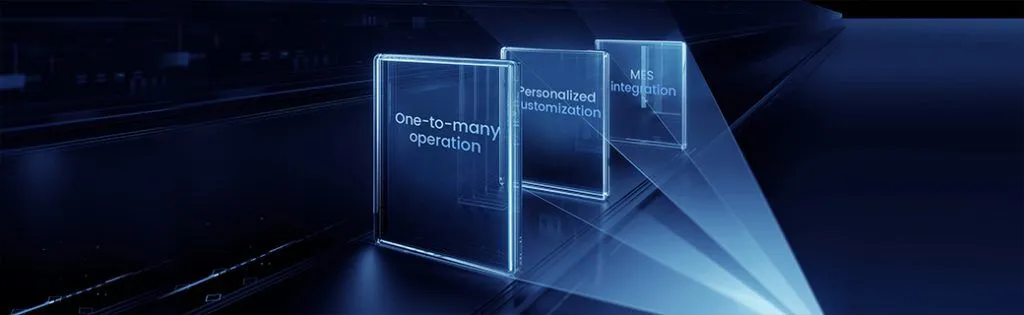
⇲ Intelligent extension
* Due to its modular-based structure, users’ personalized demands and other optional functions are also available.
* New materials and processes are permitted to use to make the production highly efficient. New welding technology also helps to get efficiency gains and high quality.
* Low-energy and low-emission devices or processes can also be utilized to minimize effect on environment and make resources recycling.
Recent Posts
Archives
Categories
Related Products
12~24 [PPM] Total capacity
≥99.5 [%] Final excellent rate
≥90 [%] Machine utilization rate
Equipment Capacity: 12~24 PPM
Overall Line Yield: ≥99%
Overall Line Utilization Rate: ≥98%

Hak Cipta © 2025 Senfeng Laser Technology Co., Ltd. Semua Hak Dilindungi Undang-Undang
Tautan terkait
Hubungi Kami
Alamat:Ruko Golf Island Blok E no 80. Kecamatan Penjaringan, Daerah khusus Ibukota Jakarta
Recent Comments