· Indonesia local stock and accessories
· Local engineers and installation team
· On-site training services in Indonesia
SENFENG provides localized services in Indonesia
Indonesia Service Hotline:0813 8899 3760
We always put fast-response service first to create more benefits for global users. Here are our 7 types of service. With these, your machine will always remain in optimal state.
New Machine Installation
Our engineers will offer on-site installation or online guidance to ensure a smooth setup of your machine.
- Foundation
Our engineers will contact the client to prepare the installation site and foundation, ensuring they have base plates ready. The base plates will be secured to the concrete floor with expansion bolts. Once the machine is leveled, the adjustable feet will be welded to the base plates for stability. Ideally, a concrete column of 500×500×400 mm should be poured under the base plates. If the floor can support approximately 5 tons per square meter, the base plates can be directly fixed to the concrete.
- Installation
The machine will be placed on the foundation and leveled. The components that were disassembled prior to shipping will be reinstalled, including the mechanical parts, sheet metal parts, power cables, signal cables, laser, and water chiller.
- Commissioning
The equipment will be commissioned to check the functionality of all signals and ensure proper operation. The parameters for the client’s required materials—such as stainless steel, carbon steel, aluminum, and galvanized sheets—will be configured.
- Training
- Machine operation explanation
- Training on cutting software basics and operation
- Cutting adjustment training
- Supervision of client’s independent operation
- Acceptance
After the machine installation is confirmed, the client should sign and stamp the following documents: Laser Equipment Installation Acceptance, Training Procedure Record, Maintenance Confirmation, and Laser Equipment Safety Operation Procedures.
Repair Service
On-site repairs during the warranty period include free shipping and spare parts (excluding consumables). Once the customer submits a repair request, we will promptly troubleshoot and provide targeted solutions.
- Diagnosis
Engineers will troubleshoot either online or on-site.
- Repair Request
After identifying the issue, a repair request will be submitted, specifying any required replacement parts along with their models and quantities.
- Dispatch
If the customer can’t resolve the issue, we will quickly send an engineer to assist on-site after the repair request.
- Resolution
The engineer will assess the problem and resolve it quickly and effectively.
- Confirmation
After the issue is resolved, the client should confirm and sign the After-Sales Service Form.
Regular Maintenance
- Cleaning
- Clean the external parts of the machine, including the keyboard, mouse, and operating platform.
- Clean the dust inside the electrical cabinet.
- Clean the industrial computer.
- Clean the guide rails of all axes.
- Clean the waste cart.
- Remove residual slag from the working platform.
- Inspection
- Check the nozzle and the protective lens.
- Inspect the ceramic ring.
- Check the air system (ensure accurate pressure control).
- Inspect the water system (check for leaks).
- Inspect the oil system (ensure adequate oil levels, proper lubrication timing, and check for leaks).
- Inspect the exhaust system (ensure vents are functioning, cylinders are operational, and air hoses are undamaged).
- Check limit switches for any damage.
- Inspect the exchange platform chain to ensure there is no looseness or damage.
- Check quick connectors and plugs for looseness.
- Inspect grounding to ensure it meets standards.
- Operations
- Perform capacitance calibration
- Change water in the chiller.
- Add antifreeze.
- Adjust water temperature in the chiller.
- Clean the water chiller filter.
- Replace the three filters in the air compressor.
- Schedule a comprehensive inspection and maintenance visit from the manufacturer.
Online Service
A professional online service team is available 24/7 to provide comprehensive support and guidance to customers.
- Dedicated Group
We create dedicated after-sales support groups for each customer, allowing them to consult directly in the group for any issues or when purchasing parts, with engineers providing timely assistance.
- Assigned Responsibilities
We will assign specific personnel for accessory and technical issues based on machine models, ensuring clear responsibilities to better assist customers.
- Real-Time Consultation
We will promptly offer precise solutions for customers to ensure timely responses.
- Regular Follow-Ups
We will follow up with customers to gather feedback, gaining deeper insights into the strengths and weaknesses of our products and services, and make timely improvements to enhance customer satisfaction.
Extensive Training Options
- On-site Learning
If customers plan to visit the factory for training, we will provide a detailed training schedule and arrange for professional engineers to conduct one-on-one workshop training. Currently, this is available in Chinese and English only.
- On-site Guidance
For on-site guidance, we will send professional engineers to train customers, following the Training Procedure Record.
- Online Service
We have a professional online after-sales service team with two modes:
- Online Support: Customers can leave messages in the group about topics they want to learn, and we will provide guidance through text, images, and videos.
- Online Video Guidance: We will arrange for professional engineers to conduct one-on-one video explanations, providing a more intuitive and quicker learning experience. Currently, this is available in Chinese and English only.
- Other Training
We will create a customized training plan for any special customer requirements.
Original Accessories
We offer a variety of laser heads from multiple brands and power levels, including Precitec, Raytools, WSX and SENFENG.
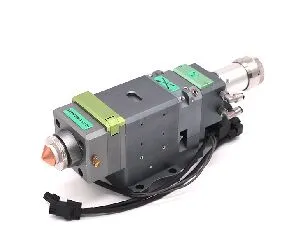
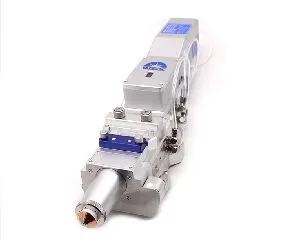
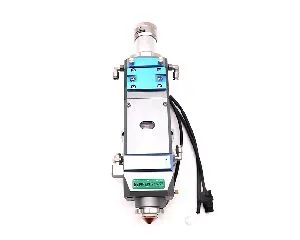